PRIMERS
Tardigrade Primers are epoxy based, two component, low viscosity, solvent free and contain trace amount of VOC. With its elastic structure and high adhesion strength, it penetrates the capillary pores in concrete, making the structure stronger.
Primers provide initial contact with the surface and are the keystone of application detail. Tardigrade Primers are produced from raw materials, which are derived from the most reliable sources in the world.
Epoxy Coatings
Tardigrade Epoxy Coatings are two component, solvent free and contain trace amount of VOC. Coatings are liquid impermeable and can be manufactured in all RAL colors. Additionally, these products are elastic in structure, resistant to chemicals and mechanical loads and have very high adhesive strength.
Epoxy Coatings, which form the final and visible layer, are the keystone of application detail. Tardigrade Epoxy Coatings are produced from raw materials, which are derived from the most reliable sources in the world.
Polyurethane Coatings
Tardigrade Polyurethane Coatings are two component, solvent free and contain trace amount of VOC. Coatings are liquid impermeable and can be manufactured in all RAL colors. Additionally, these products are elastic in structure, resistant to chemicals and mechanical loads and have very high adhesive strength.
Polyurethane Coatings, which form the final and visible layer, are the keystone of application detail. Tardigrade Polyurethane Coatings are produced from raw materials, which are derived from the most reliable sources in the world.
WATERPROOFING
Tardigrade Waterproofing Products are designed without compromising mechanical and chemical high performance features. . Consisting of many different polymer combinations, with solvent / solvent-free / water-based characters, the products designed as single and double component according to the needs of the places of use have high elongation and elasticity. Products focused on the maximum benefit to be achieved with the correct solution of waterproofing systems provide water and moisture insulation for many years.
Waterproofing products that should be planned according to different application areas and needs, Tardigrade ‘ Compatible with all other product sets. Tardigrade Waterproofing Products, produced with raw materials obtained from the world’s most reliable sources, represent the highest quality at the point of service.
POLYURETHANE/POLYASPARTIC
ALIPHATIC COATINGS
Tardigrade Polyurethane / Polyaspartic Aliphatic Coatings are two component, solvent/water based or solvent free. Aliphatic coatings have high UV resistance and can be manufactured in all RAL colors. Additionally, these products are liquid impermeable, elastic in structure, resistant to chemicals and mechanical loads and have very high adhesive strength.
The Polyurethane / Polyaspartic Aliphatic Coatings are the decorative layer and are complementary in application detail. Tardigrade Aliphatic Coatings are produced from raw materials, which are derived from the most reliable sources in the world.
REPAIR AND STRENGTHENING
Tardigrade Repair and Strengthening Products are epoxy based, solvent free and contains trace amount of VOC. They are resistant to chemicals and mechanical loads and have very high adhesive strength. By penetrating deep into the fractures and cracks on the application surface, they increase the mechanical resistance and physical strength of the surface.
Repair and Strengthening Products are used for preparation and repair purposes and are the keystone of application detail. Tardigrade Repair and Strengthening Products are produced from raw materials, which are derived from the most reliable sources in the world.
System Guidelines
Tardigrade System Guidelines have been prepared in line with the scientific data and various application conditions towards the needs and demands of the building and construction market.
All the guidelines for the coating / insulating / painting of floors and walls are based on optimization of conditions and maximization of the total benefit.
Guidelines of the Tardigrade High Performance Construction Chemicals Technical Data Sheets and the system guidelines presented in detail along with the relevant technical specifications have been put into service of the market.
All system guidelines are recommendations that can vary according to many factors.
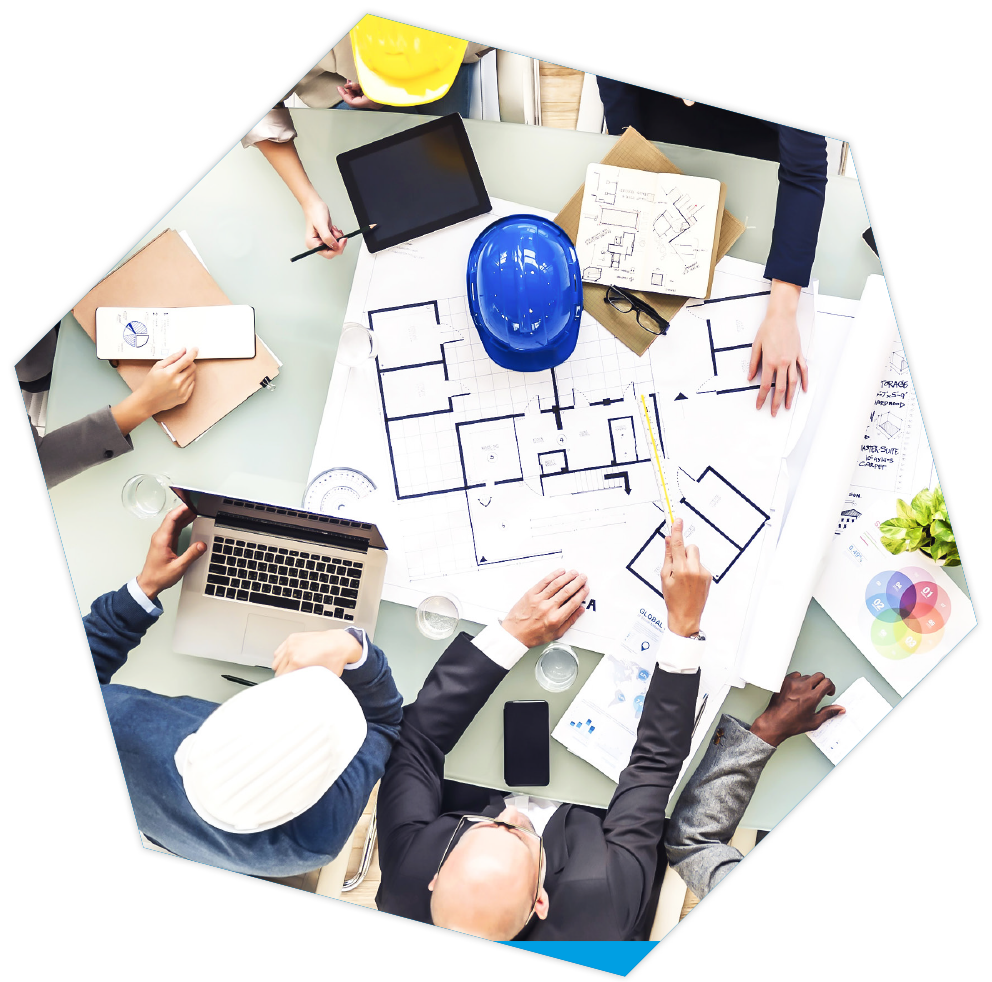
CONSTRUCTION CHEMICALS
Tardigrade Construction Chemicals is a leader in the construction chemicals sector by providing superior services and expertise through the manufacturing of epoxy, polyurethane, polyurea and polyaspartic based resin systems for the floor covering and waterproofing industry.
With offices in Turkey, Germany and the United States, Tardigrade is dedicated to the manufacturing of high-performance construction chemicals throughout the world.
Our on-site R&D facilities combined with our extensive knowledge enables us to manufacture superior products, right and on-time. Tardigrade test all of its products in accordance with ASTM, FM, UL, EN, DIN, ISO, TSE and all other international standards.
As your construction chemical partner, we constantly develop and renovate our products in order to meet both classic and special project needs. Our goal is to provide ultimate support to our consumer bases by helping our clients make the right selections based on their application needs.
COATING AND WATERPROOFINGS
Resin based product groups are widely used in building and civil engineering applications. Tardigrade partners with these sectors to provide multiple types of resins including epoxy, polyurethane, polyurea and polyaspartic based resin systems for the application of coating and waterproofing of flooring surfaces. Our applications are specifically designed and formulated to offer our customers the optimal solutions in accordance with the highest performance criteria as listed below:
- Excellent wear resistance
- Very low shrinkage during and after curing
- High mechanical strength
- Excellent adhesion ability to many different surfaces
- Wide range of applications suitable for different climatic conditions
- Easy to clean
- Aesthetic, decorative design advantage with color and pattern options
- Monolithic application with joint and joint surface to create a hygienic environment
- Long lifespan
- Resistance to thermal shocks
- High corrosion resistance
- Resistance to chemicals
- Excellent penetration and adherence properties
- High wear and impact resistance
- Fluid impermeability
- Create conductive environments with the option of anti-static properties
The purposes and areas of use of polymeric resin-based products are as follows:
- Surface protective coatings
- Waterproofing for concrete flooring and walls
- Non-slip floors with aggregate
- Repair, levelling and retrofitting mortars
- Hygienic floor and wall coverings in areas such as operating rooms and hospitals
- Pool, laundry, food storage and laboratory floor coverings and waterproofing
- Floors at factories, sports complexes, airports, parking lots, schools and shopping malls,
- For use as a decorative element
- Corrosion protection for reinforcement and steel materials
- Bonding of metal plate and concrete mounting accessories
- Bonding of stone, aluminum, tiles and wood
- Anchoring irons and sprout sowing operations in reinforced concrete
- Structural connection, repair and repair works
- Repairs of cracks and fractures
- Concrete reinforcement injection applications
- Bonding elements to connect old-new concrete
- Installation of bearing plates and connection bolts in bridges and dams
- Manufacturing and assembly of railway lines
- Joint filling of ceramic coatings that face mechanical and chemical effects
- Anti-dust agent against friction and wear
- Anchor mortars for installation of crane rails and machines
- Adhesives for structural fixation of prefabricated concrete elements
- Injection materials for maintenance, repair and strengthening
- Coatings that add design richness while providing a hygienic environment in a verity of uses
Polymeric resin technology is the standard solution around the world offering numerous coating and waterproofing applications. The main technical features of polymeric resin-based products are as follows:
- Density
- Viscosity
- Short A/Short D hardness
- Compression strength
- Bending resistance
- Adhesion strength
- Wear resistance
- Elongation
- Solid matter ratio
- Remaining time of use after mixing
- Full curing time
FEATURES OF EPOXY SYSTEMS
Epoxies have excellent resistance to wear. Wear resistance of a given system depends on the quality of the product group and application as well as the management of environmental factors.
Epoxies have a very good adhesion strength compared to almost all materials used in construction. Cement and mineral based surfaces (concrete/screed), metal, glass and ceramic surfaces are adhesion resistant. In order for epoxy systems to adhere, the application surface must be prepared properly.
This includes priming of the applications surface whether it be a floor or wall. Prior to applying any finished materials, it is recommended to perform an adhesion test, or pull off test, to ensure the final result. Test are conducted in accordance with ASTM D-4541 methods.
The quality of epoxy systems can be attributed to low hardening shrinkage, long-term dimensional stability, high stress and compressive strength, moisture and resistance to chemicals.The mechanical and chemical resistance of epoxy systems is directly related to the type and formula quality of the raw materials used.
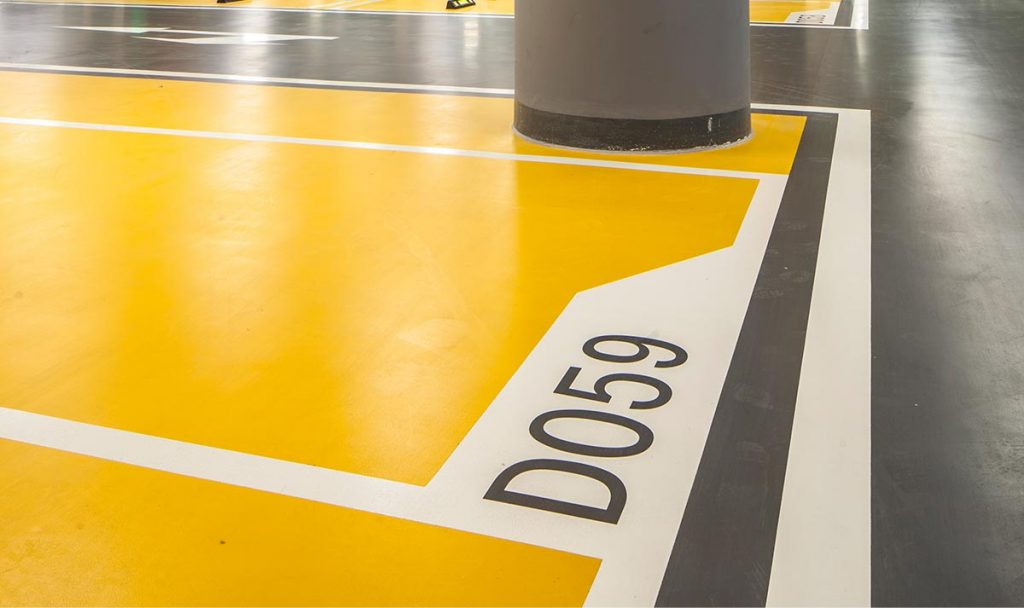
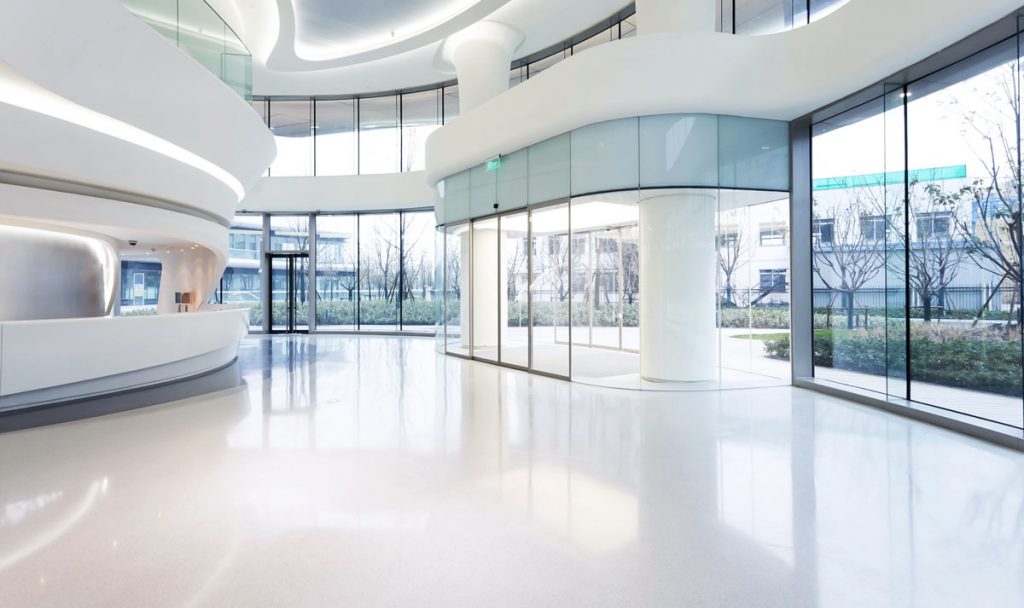
Epoxies are excellent electrical insulators. By increasing the polarity of the molecules, their electrical waterproofing properties are reduced. The addition of metallic fillers, metallic wools, carbon black, and conductive chemical additives transforms the nonconducting epoxy formulation into an electrically conductive system. Nonconducting fillers increase arc resistance and, to some extent, raise the dielectric constant.
Epoxy systems with appropriately selected chemical fillings show high resistance to rapid changes in temperature and shows no signs of cracking or fragmentation when designed correctly. Epoxy systems with low elasticity can cause serious problems on reinforced concrete structures. Better formulated systems can withstand repeated thermal shock cycles from 180°C to -75°C.
With high temperature aging, epoxy systems often show loss of power, decline in properties and crispness due to loss of volatile parts. Further increases in temperature can result in charring followed by cracking and weathering.
Epoxy coatings are considered a versatile option for the construction industry due to their excellent adhesion to concrete, steel and metal surfaces. The protective properties resist chemicals and corrosions, while being tough with little physical impacts.
Epoxies, which provide excellent results especially for indoor applications, are not suitable for direct external uses due to their yellowing and chalking tendencies when exposed to sunlight.
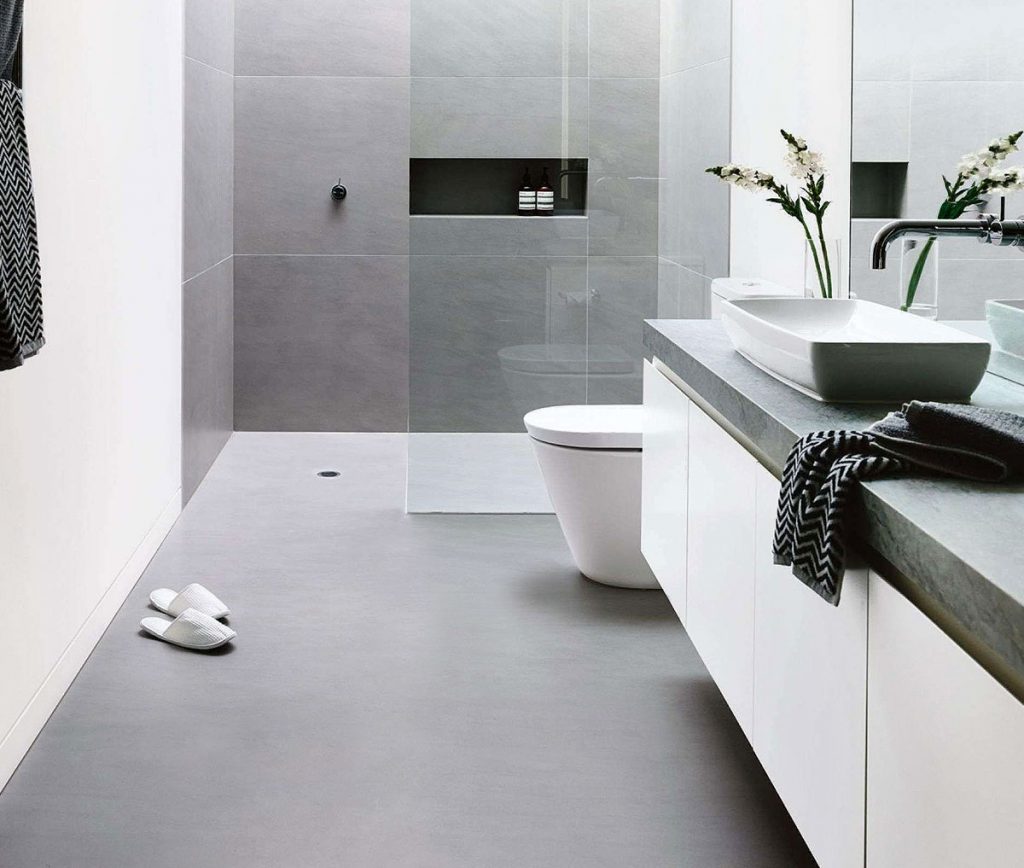
Outdoor coatings however, need to be used in combination with aliphatic polyurethane or polyaspartic staining solid which will provide UV resistance. Epoxy coating can be reinforced by laminating with glass fiber to increase thickness or to bridge fine cracks in substrates when necessary.
Some epoxy product groups are also formulated with moisture tolerance for use on concrete surfaces with high humidity.
PROPERTIES OF POLYURETHANE SYSTEMS
Polyurethane is a polymer consisting of a chain of organic units combined with carbamate connections, as known as urethanes and are classified according to
their level of flexibility. Curing of polyurethanes generally takes anywhere from 24 – 72 hours, of which a very solid polymer structure is obtained. Technological developments in this sector have paved the way for more robust and more flexible coating and waterproofing systems to emerge.
Polyurethane resins are used to protect against environmental conditions such as rain, wind, storms, sun, thermal changes, air pollution, chemical effects, and more. In addition to protecting, they are used to insulate and provide a decorative finished to the outside of building in an effort to prevent mechanical, physical and chemical changes to the facade.
These protective, paintable coatings consist of two liquid components; polyurethane resin and isocyanate. When mixed together, in the right portions, an exothermic reaction will occur causing the chemicals to slowly cure and harden.
Once the products have hardened, the coating creates an insulating bond. It is important to understand the process of curing. The first stage of this process is called gelling or jamming. The gelling mixture gradually will become a solid surface as it continues to harden.
The hardening process is also known as curing. Curing times vary depending upon the outside temperature and humidity in the air. Temperature changes affect curing processes as well as viscosity and rheological values of the product by changing a relative effect on application results. Therefore, the application is not recommended in weather conditions below +10°C above +30°C and in rainy weather.
Cured polyurethane coatings have extremely strong adhesion strength and are an excellent method for waterproofing.
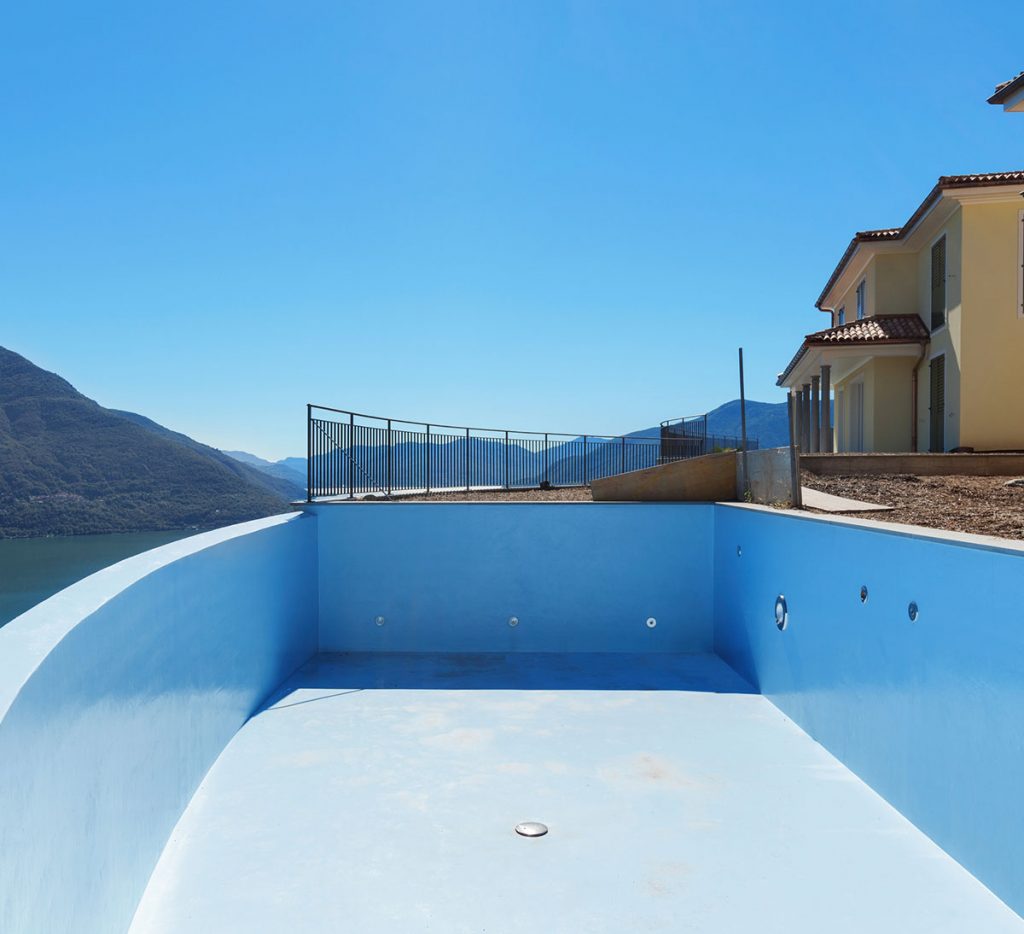